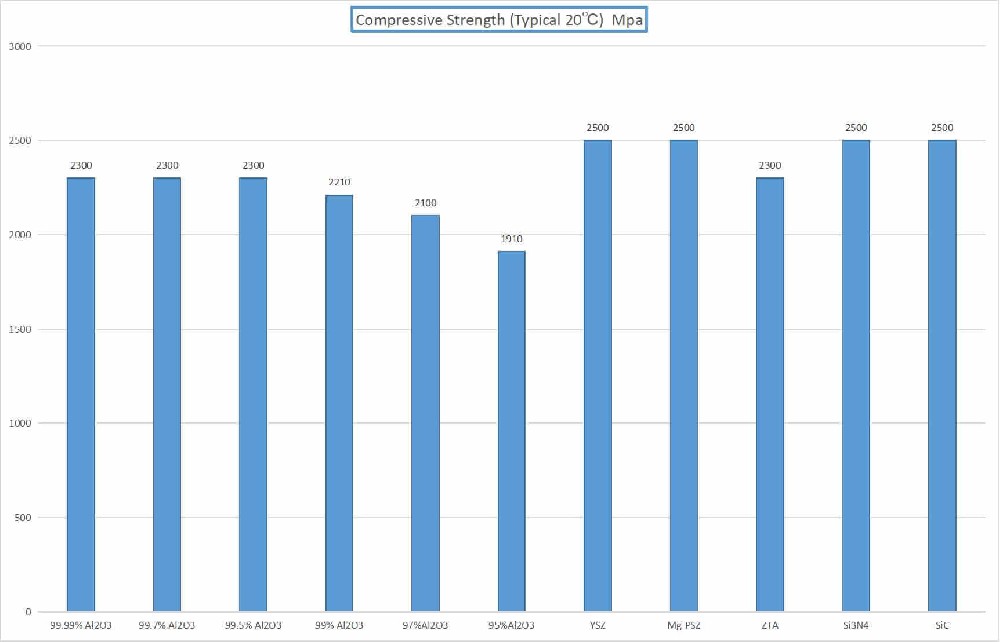
Ceramic Compressive Strength
The strength of ceramic materials varies according to the type and manufacturing process, ordinary ceramic products can usually withstand a pressure of about 5 mpa, and special ceramics such as alumina, zirconia and silicon nitride, its strength can reach several 2000-4000MPa. These numerical differences are mainly due to the microstructure and chemical bonding properties of ceramic materials. The specific pressure needs to be determined according to the type of ceramic and application scenario.
Compressive strength of various ceramics:
(1) Alumina ceramics: Through high thermal stability, high hardness and excellent performance, it is often used to manufacture various parts in high temperature environment. Its strength range is wide, ordinary alumina ceramics can reach 50-100 mpa, and high-strength alumina materials can even reach more than 200 mpa.
(2) Zirconia ceramics: because of high hardness, high thermal stability and very low coefficient of friction and favored, often used in high-end aerospace devices and other manufacturing. Its strength is generally high, ordinary zirconia materials can reach 70-120 mpa, high-strength products can reach nearly 200 mpa.
(3) Silicon nitride ceramics: known for high hardness, oxidation resistance and other properties, often used in high temperature applications such as the manufacture of thermal conductivity components. Its strength is also relatively high, ordinary silicon nitride materials can reach 50-80 mpa, high-strength products can reach about 120 mpa.
The compressive properties of ceramics are determined by their microstructure characteristics. Its crystal structure is relatively stable, not easy to deformation and damage, so it has a strong ability to resist pressure. At the same time, ceramics can also withstand higher temperatures and pressures, so they are often used in some high-temperature and high-pressure environment applications.
Influencing factors of compressive properties
1. Elemental composition: The composition of ceramic materials directly affects its compressive performance. In general, elements with higher hardness can improve the compressive properties of ceramic materials. For example, the silicon carbide composition in silicon carbide ceramic materials gives it excellent compression resistance.
2. Structural design: The structural design of ceramic materials is also one of the key factors affecting the compressive performance. Reasonable structural design can improve the strength and stability of ceramic materials. For example, the compression properties of ceramic materials can be improved by adding particulate reinforcers.
3. Texture defects: Texture defects in ceramic materials will also have a certain impact on compressive performance. For example, defects such as voids and pores can reduce the compression resistance of ceramic materials. Therefore, when preparing ceramic materials, attention should be paid to reducing the occurrence of texture defects.
Test method for compressive performance
Commonly used test methods include compression test and Young's modulus test. The compression test evaluates the compressive resistance of a ceramic material by applying a force perpendicular to its surface. Young's modulus test is to evaluate the compressive performance of a material by measuring the relationship between strain and stress during compression. These two test methods can accurately evaluate the compressive resistance of ceramic materials.