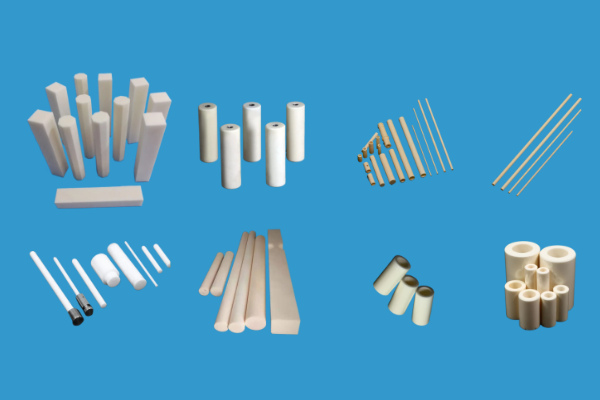

ceramic parts
Ceramic parts customized machining ceramic structure components
Structural ceramic parts have superior strength, hardness, insulation, thermal conductivity, high temperature resistance, oxidation resistance, corrosion resistance, wear resistance and other characteristics, showing high stability and excellent mechanical properties under very harsh environmental or engineering application conditions. Especially in the environment of mechanical components or electronic components with high precision, high wear resistance and high reliability, structural ceramic parts are more efficient and longer in use than parts of other materials, and structural ceramic parts are more time-saving and cost-saving.
Common ceramic parts and ceramic machining categories
1. Machining ceramic material category:
Alumina ceramics, zirconia ceramics, silicon nitride ceramics, aluminum nitride ceramics, silicon carbide ceramics, boron nitride ceramics and machinable ceramics.
2. Ceramic color routine:
White ceramic, black ceramic, blue ceramic, light yellow ceramic
3. By use:
High temperature resistant ceramic parts, wear-resistant ceramic parts (structural parts), insulating ceramic parts, high toughness ceramic parts,
Ceramic parts include ceramic fixing knife, ceramic tube, ceramic rod, ceramic substrate, ceramic plate, ceramic positioning pin, ceramic plunger, ceramic pump valve and other types of ceramic structural parts, widely used in melting furnace, semiconductor, aerospace, pump valve, new energy, fluid control and other fields, mechanical wear parts.
Commonly used molding equipment includes isostatic pressing, dry pressing, injection molding, etc., sintering equipment has lifting furnace, push plate kiln, etc., machining equipment includes internal and external circular grinding, surface grinding, centerless grinding, fine grinding, CNC engraving machine, laser cutting machine, etc., testing equipment has Sanfeng micrometer, Sanfeng caliper, Sanfeng roughness detector, projector, density detector, etc. Height gauge, magnifying glass, etc.
Some of our ceramic parts on display
ceramic tube parts
Perpendicularity 0.01, concentricity 0.01
ceramic rod bar parts
Roundness 0.005, straightness 0.005
ceramic plate parts
The dimensional tolerance of machined parts is up to 0.001
ceramic bushing parts
Outer diameter 1-100mm, inner diameter 0.1-80mm
machinable ceramic parts
The surface roughness Ra is 0.02-0.1μm
ceramic ring parts
Chief operating
ceramic liner parts
Caliber 100mm-- 650mm, length 100-- 1600mm, wall thickness 5-- 300mm
custom ceramic parts
Finish less than Ra0.02
Precision machining of ceramic parts
The precision machining process of industrial ceramic parts includes precision cutting (such as diamond boring, precision turning, wide-edge finishing planing, etc.) and high finish and high precision grinding. The machining accuracy of precision machining is generally 10-0.1μm, the tolerance level is above IT5, and the surface roughness Ra is below 0.1μm.
- Dimensionalaccuracy:Upto 0.001mm
- Concentricity:Up to0.003mm
- Parallelism:Up to 0.002mm
- The inner hole tolerance:The minimum machinability is 0.005mm
- The linear tolerance:Up to 0.001mm
- Straight flute:The narrowest machinable groove width is 0.1x100mm
- The thickness of the size:Minimum machinability to 0.02mm
- Cylindricity:Up to 0.004mm
- The smallest aperture:The minimum capacity is 0.07mm
Ceramic parts machining process
The machining process of ceramic parts mainly includes three stages: roughing, semi-finishing and finishing.
- 1. Roughing stage: The use of milling, turning and other traditional machining methods to remove most of the margin, so that the parts close to the final shape. Due to the hardness and brittleness of ceramic materials, it is necessary to select the appropriate tool and cutting parameters during roughing to avoid tool wear and parts breakage.
- 2. Semi-finishing stage: on the basis of rough machining, further adjust the shape and size of the parts. At this stage, grinding, grinding and other methods can be used to obtain higher surface quality and accuracy. At the same time, it is also necessary to pay attention to controlling the machining temperature and the use of coolant to prevent the generation of thermal deformation and cracks in the material.
- 3. Finishing stage: After the shape and size of the parts are basically determined, finishing is carried out to improve the surface quality and accuracy of the parts. Finishing methods include ultra-fine grinding, polishing and grinding. At this stage, special attention needs to be paid to the selection of tools during machining, the adjustment of cutting parameters and the control of the machining environment to ensure the machining quality and efficiency of the parts.
Contact Form
Tips:If you have any questions, please contact us, we will get back to you within 1 hour.